Product Design Engineering
As an engineer, I have worked on bringing both simple and complex design projects to life. Acting as the voice of the customers, and resolving both design and engineering issues as they arise in design and product development.
Servi Plus & Servi 2.2 Suspension Retrofit (d. 2022)
Joined the team as engineering program manager to support the development of next generation of service robots. Work along side ME, EE, FW, Navigation, and SCM to choose the new camera models & locations for servi plus to ensure best coverage and reduce blind spots. Worked closely with mechanical engineering team to redesign EVT prototypes to go into DVT stage. Facilitated communication between US and KR R&D team to ensure design convergent and de-risk engineering challenges. Extensive review with ID team on plastic DFM and tooling review before kick-offs.
Worked closely with KR side engineering to enable Servi 2.2 Suspension Retrofit to improve Servi’s ramp and threshold performance by generate formal design documentation, hold design reviews, conduct prototype validations, and SOP control and prepare the readiness of production.
4U Superblade Double Width (d. 2022)
Led design effort on 4U Superblade double width system and complete chassis and enclosure redesign to allow backward compatibleness with single width blade chassis. Responsible for system architecture and build plans to enable Generation 13 motherboard supporting 4th Gen Intel Xeon Scalable processors with new air cooling heatsink and passive liquid cooling module.
Worked closely with vendor to define package design that will pass ISTA drop test standards for both enclosure and double Width.
Worked with EE team to develop the new backplane for the double width config and troubleshoot flatness and connector alignment challenges.
Worked closely with thermal team to developed air shrouds for double width config to de-risk thermal challenges due to air leak and inefficient air circulation.
MicroBlade HDD bracket & SlimSAS Cable (d. 2021)
Led design effort on HDD bracket and SlimSAS Cables for new generation of product. Designed a backward compatible HDD bracket and reduced tooling cost by using existing tooled bracket material. Redefined PCB layout to avoid interference. Instructed cable vendor to prototype SlimSAS Cable for cable length and worked with internal lab department for system validation. Reduced risk of interference and mechanical issue using tolerance analysis for heatsink stack up.
8U SuperBlade with Direct Liquid Cooling (d. 2021)
Owned the product development process as the mechanical lead with cross-functional team to integrate Direct Liquid Cooling into existing node chassis design. Collaborated closely with liquid cooling solution vendor to spec in and built early prototypes for system validation and environmental testing. Led the design of I/O bracket for liquid cooling supply/return tubes and responsible for board-level design of a fan control Add-on-Card module with 5-pin fan connectors to enable detail pump reading from the cold plates. Managed multiple vendors for component readiness and worked closely with Asian Team to transfer production to Asia by providing SOP and trainings and successfully shipped 2000+ units for early deployment at customer site.
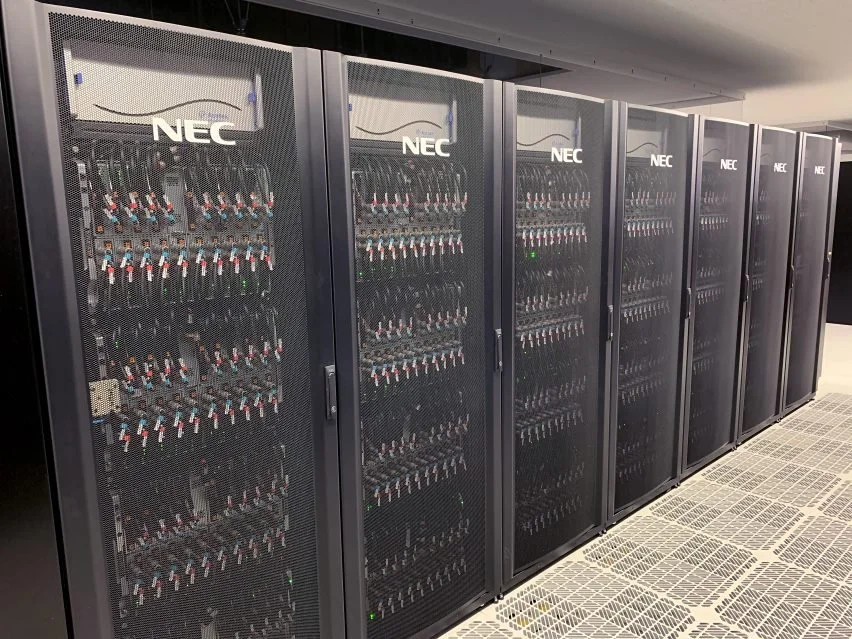


8U SuperBlade HDR 200G Network Switch (d. 2020)
As the mechanical lead for the product, and provided both technical and project management to ensure supplier readiness. The first in the company to enable OverPass QSFP+ connectors design to allow total of 20 ports on a pre-existing chassis platform to meet product spec (4 more ports than the last generation). This product architecture allowed taller and bigger heatsink which improved thermal performance of the mellanox quantum HDR switch IC. Enabled new Midplane connectors with foolproof mechanism due to product generation incompatible challenges. Designed chassis with mechanical brace on both switch and add-on-card to improve reliability of the high speed Midplane connectors due to compliant pins design trade-offs. Responsibled for driving the system level shock and vibration analysis and validations.
Die Cast Housing Yield Rate Improvement (d. 2019)
Worked closely with die casting factory to drive DoE to improve yield rate. Flatness was required to be 0.30 mm on the bottom surface (datum reference plane) of the housing, and only about 5% are meeting the flatness tolerance after bead blasting process. During observation many housing came out of the die casting mold with more than 0.3 mm flatness, so a reshaping process was put in to improve the yield rate, which increased the failure rate. Multiple DoE was conducted with different bead blasting material ranging from 80 lb. grit to 120 lb. grit. FEA simulation supported the assumption the causation of the distortion was due to lack of structural support and irregrulation of the unit wall and not able to withstand the bead blasting process, so a fixture was introduced to support the unit during beed blasting process to remove the need of a second reshape process after bead blasting.
UVA LED 450nm & 405 nm single board + thermal management system (d. 2019)
Working with Violumas, a UV LED company under Cofan Group, we built a prototype that can host both 450nm and 405nm UVA in one single board. Violumas used Flip Chip Opto’s patented 3-PAD technology to efficiently bring heat to the heat spreader. A thermal management with active cooling system that unitized fans was selected for this application. For a small prototype run of one unit, the heatsink was manufactured using CNC machine and bonded using epoxy. I worked on providing the final system 3D model and work closely with the thermal engineer for the project.


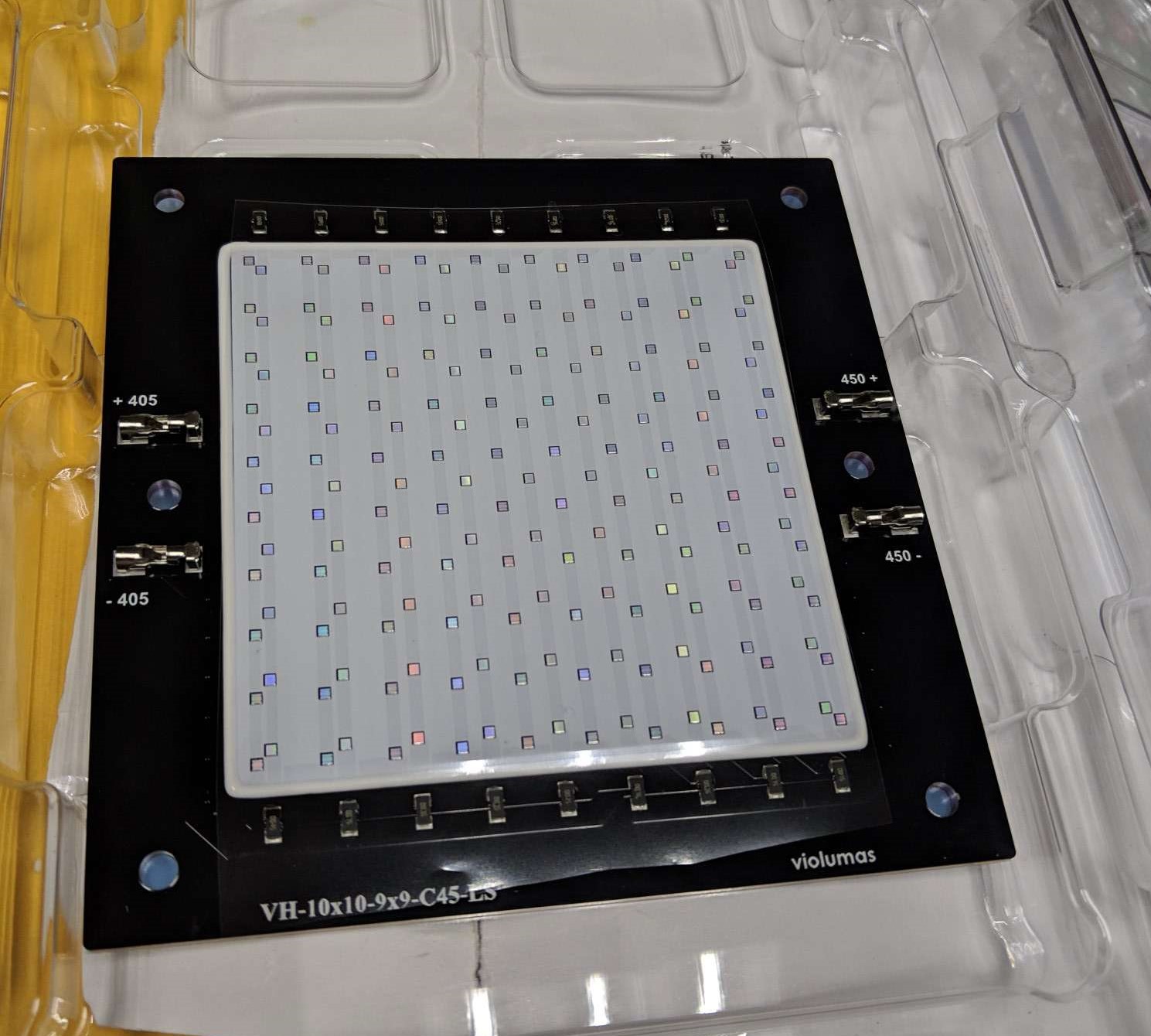

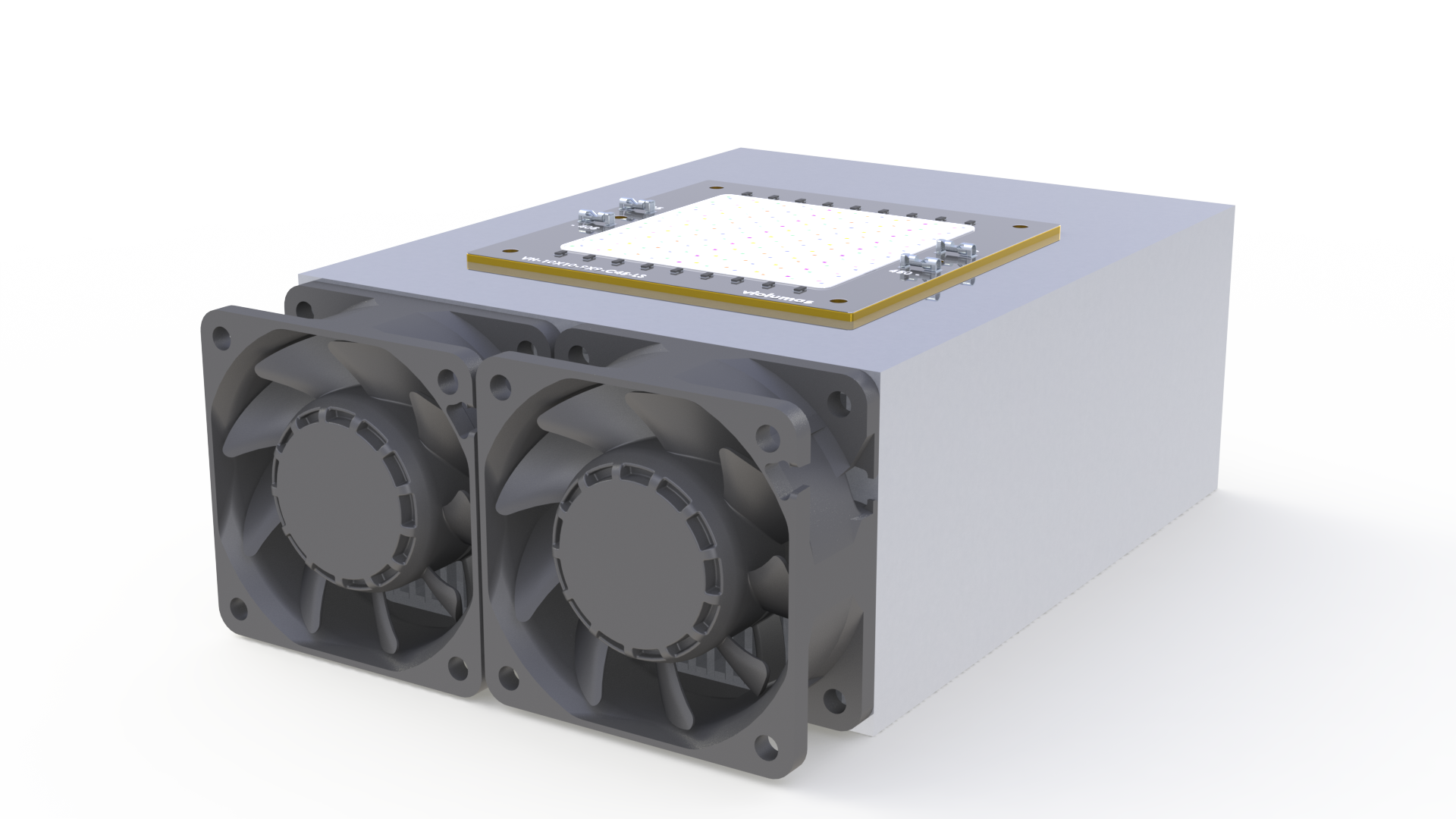
High Temperature Range Fan (d. 2018)
A customized solution of a high temperature fan. The existing products on the market didn’t satisfy our customers needs. We took the best product existing on the market and improved upon. I was involved in the product design & realization and worked closely with our Asia based team on the fan spec and move into prototype and testing. I heavily involved in product development and product marketing of the product. Research was done to understanding the market and the possible applications that need a fan to withhold such high temperature.
FEATURES
Wide temperature range: -40°C to +130°C
Expected life: 50,000 hours 90°C**
KEY COMPONENTS
Blade: 185℃
Frame housing: ADC 12
Ball Bearing: 180-230℃
Driver IC: 105℃
APPLICATIONS
Semiconductor equipment
High lumen laser projectors
PV Inverters




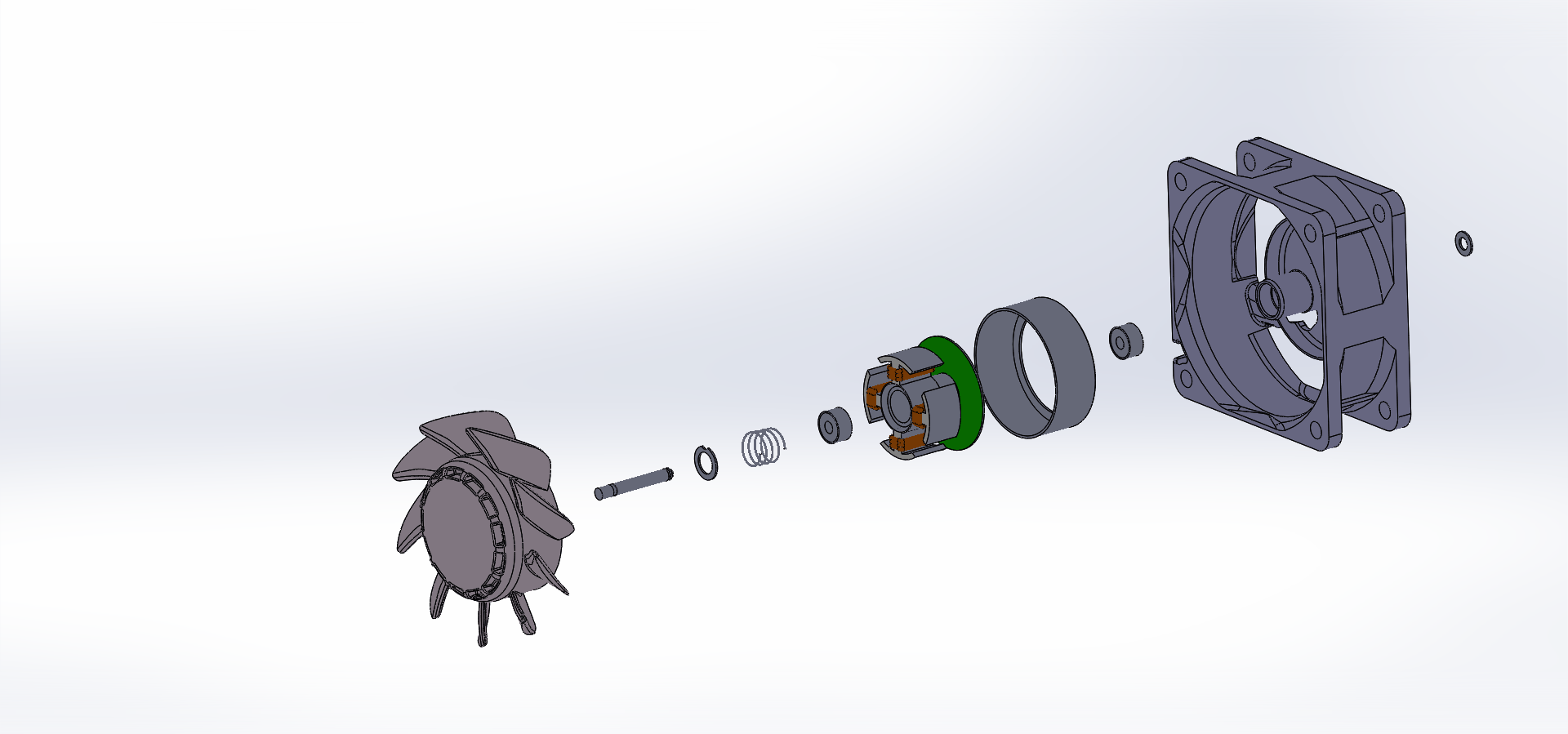
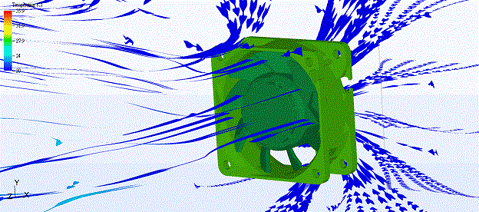
Wrist strap design for a medical device (d. 2018)
I worked with a small medical device company to design their wrist strap. The device is about 300 grams and similar to the size of iPhone 8+. The wrist strap will be possibly in contact with body bodily fluids and will be sanitized with hydrogen peroxide & withhold a temperature higher than 121˚C. I recommended silicone due to the following properties:
Low thermal conductivity
Low chemical reactivity and toxicity
Thermal stable up to 250˚C
Does not support microbiological growth
Various cleaning methods: ethylene oxide, autoclave, gamma radiation, and e-beam radiation
The final design was a one-piece design without any plastic detachable connectors to avoid glue and other plastic materials with lower melting points. I also worked with the manufacturing team to source vendor, and material spec for the part. I worked with the vendor to obtained MSDS report and approved the final drawing for the tooling.
COB Grow Light - Duet Fixed Series (d. 2019)
Working with Flip Chip Opto and taking 2D CAD drawings of the COBs and turning them into 3D model for the grown light series. The Duet series offer red and blue on the same board to correspond to various plant growth stages. The series features 60W to 300W and 5 different PPFD rations between 450nm Blue, and 600nm to 700nm broadband red. Each COB is structured using the patented DBR LED Flip Chip and the in-house proprietary low temperature bonding technologies.



Modeling Computer Mouse Surface (d. 2015)
This was a practice to learn how to use Soilworks Surface Modeling in Soildworks.
Geneva Gear 3D (d. 2019)
In the process of studying different classic mechanisms and mechanical devices, Here is my attempted to make my own vesion of Geneva Gear. One of the big mistake in the process of making this 3D model was not to draw it out and do the calculation before starting creating the parts in Soildworks. The second day, I did the math by define and calculate the relationship before the two parts. To minimized the sliding motion which puts way to much stress on the inner circle of the driver, I designed a three-pin driver. Motion study was successful after I made the the driven part’s diameter smaller and the radius of the cut out from 12nm to 14nm.